環(huán)模的力學(xué)性能是影響環(huán)模使用壽命的重要因素,對(duì)環(huán)模進(jìn)行力學(xué)分析具有重要意義。為了減少環(huán)模磨損,延長環(huán)模使用壽命,分析壓塊機(jī)環(huán)模工作中受力情況十分必要。目前的研究集中在對(duì)環(huán)模顆粒機(jī)的多排圓孔形環(huán)模受力分析,對(duì)環(huán)模壓塊機(jī)的單排方形模孔環(huán)模受力分析較少。該文在對(duì)研究顆粒機(jī)環(huán)模的基礎(chǔ)上研究壓塊機(jī)環(huán)模在壓塊過程中的受力,明確壓塊機(jī)環(huán)模關(guān)鍵受力部位的受力情況。應(yīng)用ANSYS軟件研究該部位在工作過程中的應(yīng)力分布及形變,為降低壓塊機(jī)環(huán)模磨損,優(yōu)化環(huán)模結(jié)構(gòu)提供一定依據(jù)。
1、壓塊機(jī)環(huán)模結(jié)構(gòu)及工作原理
環(huán)模秸稈壓塊機(jī)的環(huán)模為單列方形模孔結(jié)構(gòu),模孔通常為方形,橫截面的對(duì)角線一般大于25mm,長度不等。壓塊機(jī)環(huán)模如圖l所示采用合金鋼整體鍛造環(huán)模坯,然后用鉆頭加工多個(gè)圓孔,再用銑刀銑削使圓孔成為方孔。
環(huán)模壓塊機(jī)主要工作部件是由固定的單列方模孔的環(huán)模和轉(zhuǎn)動(dòng)的偏心壓輪組構(gòu)成。粉碎后的秸稈物料經(jīng)喂料口進(jìn)入環(huán)模與壓輪組間的成型腔中,隨著壓輪組主軸體轉(zhuǎn)動(dòng)將物料布滿環(huán)模內(nèi)表面的溝槽中,偏心壓輪沿著環(huán)模溝槽內(nèi)切公轉(zhuǎn)和摩擦自轉(zhuǎn)將物料擠壓進(jìn)環(huán)模孔。壓輪組每完成一次公轉(zhuǎn)周期就將布滿環(huán)模溝槽內(nèi)的物料擠壓人模孔內(nèi),從而形成了燃料塊的一個(gè)壓層。隨著物料的不斷喂入和壓輪組的公轉(zhuǎn)、自轉(zhuǎn),便接連不斷地形成無數(shù)個(gè)物料壓層,相繼地?cái)D入模孔中,通過模孔中不斷擠出成型。
2、環(huán)模工作受力分析
環(huán)模壓塊機(jī)的擠壓成形過程建立在物料間存在間隙的基礎(chǔ)上,通過壓輥與環(huán)模在溫度、摩擦力和擠壓力等綜合因素的作用下使物料間隙縮小,最終形成具有一定密度和強(qiáng)度的壓塊。根據(jù)物料在擠壓過程中不同的狀態(tài),壓塊過程中受力情況可分為3種過程,即供料、變形壓緊和擠壓成形,其中在擠壓成形過程時(shí),物料所受到壓輥的擠壓力足以克服物料受到模孔對(duì)其的摩擦力阻力從而擠出成型。對(duì)壓塊過程中環(huán)模內(nèi)表面和孔壁受力情況進(jìn)行分析,進(jìn)而研究環(huán)模模孔間主要受力的楔形部位受力。
2.1環(huán)模內(nèi)表面受力分析對(duì)環(huán)模在工作過程中內(nèi)側(cè)受力情況進(jìn)行研究,環(huán)模與壓輥在無物料時(shí)是存在一定間隙的,環(huán)模在生產(chǎn)壓塊過程中,壓輥和環(huán)模內(nèi)表面間隙被物料所填充,環(huán)模內(nèi)表面主要受到壓輥通過物料傳遞的擠壓力,壓輥旋轉(zhuǎn)通過物料傳遞的摩擦力。
環(huán)模壓塊機(jī)工作過程中,環(huán)模固定在機(jī)體上,偏心壓輥通過繞主軸公轉(zhuǎn)的同時(shí)自轉(zhuǎn)將物料分布在環(huán)模的內(nèi)側(cè)并通過模孔擠壓成型。對(duì)環(huán)模壓塊過程中的受力進(jìn)行分析,環(huán)模在壓塊過程中內(nèi)側(cè)受力情況如圖2所示,壓輥組在主軸電機(jī)驅(qū)動(dòng)下公轉(zhuǎn)產(chǎn)生轉(zhuǎn)矩r,壓輥邊緣在直徑為D的圓周上旋轉(zhuǎn)產(chǎn)生對(duì)物料的驅(qū)動(dòng)力Q,壓輥與物料和環(huán)模間相互作用產(chǎn)生周期性擠壓力Ⅳ并通過物料傳遞至環(huán)模內(nèi)表面,當(dāng)壓輥與物料接觸時(shí)壓輥受到物料摩擦阻力F而自轉(zhuǎn)。
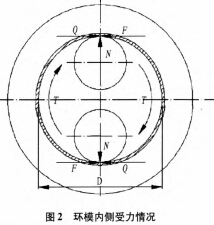
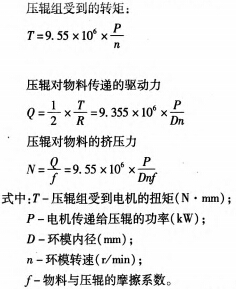
通過對(duì)在壓塊過程中環(huán)模內(nèi)側(cè)受力分析可知,在環(huán)模固定,壓輥驅(qū)動(dòng)擠壓的環(huán)模壓塊機(jī)工作過程中環(huán)模內(nèi)表面受到壓輥通過物料傳遞的軸向擠壓力與周向摩擦力的影響,通過轉(zhuǎn)矩公式得出環(huán)模內(nèi)表面受軸向擠壓力的計(jì)算公式,環(huán)模所受到的軸向擠壓力與環(huán)模的功率、環(huán)模的內(nèi)徑、轉(zhuǎn)速及摩擦系數(shù)有關(guān),再根據(jù)正壓力與摩擦力的關(guān)系求出環(huán)模內(nèi)表面所受摩擦力。
2.2環(huán)模孔內(nèi)受力分析環(huán)模壓塊機(jī)在壓輥的作用下將物料通過模孔擠出成型。在擠壓過程中,物料在模孔內(nèi)受到壓輥傳遞的軸向擠壓力,同時(shí)物料受到環(huán)模孔壁對(duì)其的摩擦阻力。模孔中的物料擠出需要滿足的條件是物料所受的軸向擠壓力大于物料與環(huán)模孔壁間摩擦力。為研究壓塊過程中方形模孔內(nèi)表面的受力情況,壓塊過程中孔內(nèi)的物料壓塊視為整體,受力分析如圖3所示。
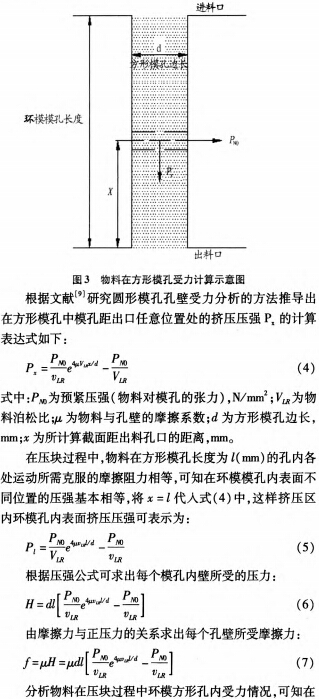
分析物料在壓塊過程中環(huán)模方形孔內(nèi)受力情況,可知在壓塊過程中模孔內(nèi)壁主要受到物料對(duì)其的擠壓力和摩擦力,擠壓力與模孔的結(jié)構(gòu)特性和物料的屬性有關(guān)。
2.3關(guān)鍵部位受力分析經(jīng)過對(duì)壓塊機(jī)環(huán)模內(nèi)側(cè)及模孔在工作過程中所受物料的作用力研究,可知在進(jìn)行壓塊時(shí)環(huán)模受到壓輥通過物料傳遞作用于內(nèi)表面的軸向擠壓力和周向摩擦力,環(huán)模的模孔內(nèi)壁受到物料對(duì)其的擠壓力以及摩擦力的影響,而這些力主要作用于模孑L間的楔形部位,楔形部位為壓塊過程中的關(guān)鍵受力部位,該部位當(dāng)壓輥運(yùn)動(dòng)到上方時(shí)受力達(dá)到最大,其受力情況如圖4所示,楔形部位受到壓輥通過物料傳遞的周期性軸向擠壓力N和摩擦力F,物料在模孔中對(duì)其側(cè)壁的擠壓力H和摩擦力f。
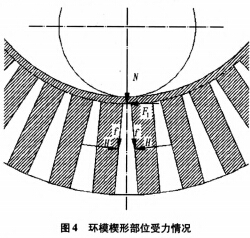
3、仿真
壓塊機(jī)的環(huán)模在壓輥對(duì)物料周期性壓縮的作用下產(chǎn)生接觸擠壓應(yīng)力,環(huán)模在此應(yīng)力循環(huán)作用下楔形部位所受局部載荷很大。經(jīng)過對(duì)環(huán)模的受力分析可知環(huán)模的楔形部位所受載荷的情況,為驗(yàn)證該部在壓塊過程中是否滿足設(shè)計(jì)要求,并研究該部位在在受力后的磨損情況,應(yīng)用ANSYS軟件對(duì)楔形部位進(jìn)行靜力分析,研究楔形部位在壓塊過程中受力后的應(yīng)力分布和發(fā)生的形變。
以生物質(zhì)秸稈壓塊成套設(shè)備數(shù)據(jù)模擬進(jìn)行仿真分析,成型機(jī)電機(jī)轉(zhuǎn)動(dòng)功率P= 45 kW,成型機(jī)額定轉(zhuǎn)速n=166r/min,成型機(jī)模孔數(shù)量為36個(gè),模孔規(guī)格為32 mm x32 mm方形模孔,成型模孔深Z= 130 mm,成型環(huán)模內(nèi)徑為D=493mm,壓輪個(gè)數(shù)為2,壓輪與環(huán)模間間隙1mm,物料與壓輥的摩擦系數(shù)為,=0.6。物料的泊松比=0.3,物料與環(huán)模的摩擦系數(shù)為p=0.38,物料預(yù)緊壓強(qiáng)(物料對(duì)模孔的張力)根據(jù)武凱等人所做試驗(yàn)得出結(jié)果為PNO=4.8 KPa。環(huán)模的材料選用45號(hào)鋼,彈性模量為210CPa,泊松比為0.3。
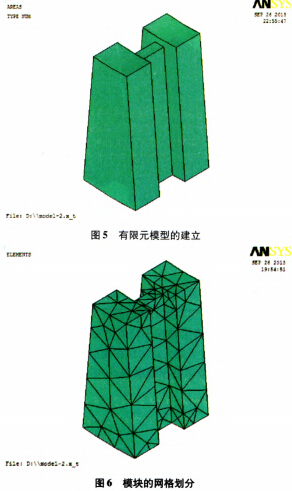
3.1模型建立及網(wǎng)格劃分為分析壓塊機(jī)環(huán)模楔形部位在工作過程中所受應(yīng)力及形變,將環(huán)模整體拆分為如圖5所示的局部模塊進(jìn)行ANSYS分析。
在ANSYS13.0中對(duì)原有的單元類型進(jìn)行了整合,該模塊選取設(shè)置網(wǎng)格類型為SOLID185單元進(jìn)行劃分,劃分后如圖6所示,并定義模塊的材料屬性,彈性模量為210 GPa,泊松比為0.3。
3.2加載載荷及求解根據(jù)環(huán)模工作原理,模塊在仿真過程中約束添加在模塊外側(cè)表面,結(jié)合壓塊機(jī)工作過程中受力情況,模塊受到壓輥通過物料傳遞的軸向擠壓載荷和周向的摩擦載荷,載荷添加在模塊楔形部位的上表面,同時(shí)也受到模孔內(nèi)物料對(duì)模塊側(cè)壁的擠壓載荷和摩擦載荷,載荷施加在楔形部位的兩個(gè)側(cè)面,載荷數(shù)據(jù)根據(jù)前文參數(shù)計(jì)算得出。
通過應(yīng)力云圖分析其結(jié)果表明,環(huán)模的楔形部位所受最大應(yīng)力為155 MPa,由于45號(hào)鋼力學(xué)性能為抗拉強(qiáng)度不小于600 MPa,屈服強(qiáng)度不小于355 MPa,楔形部位滿足使用要求。再根據(jù)如圖8所示形變圖觀察其形變位移。
由模塊楔形部位形變圖可知楔形部位在壓塊過程中受力最大形變位移量為0.015 6mm,形變量較小,不影響物料通過環(huán)模擠壓成型。
3.3結(jié)果與分析通過對(duì)模塊的楔形部位進(jìn)行ANSYS分析,可知在壓塊過程中環(huán)模的楔形部位受力后的軸向應(yīng)力分布。應(yīng)力沿軸向不均勻分布且越與壓輥接近所受到的應(yīng)力越大,應(yīng)力最大點(diǎn)出現(xiàn)在楔形部位兩端與環(huán)模整體相接處,將會(huì)造成該處出現(xiàn)磨損,在壓輥周期性載荷作用下易引起疲勞斷裂。
楔形部位在壓塊過程中受力后發(fā)生了變形,形變位移沿切向呈不均勻變化,中間位移量較大兩端較小,位移方向與壓輥運(yùn)行方向相關(guān),最大位移出現(xiàn)在楔形部位頂端,將造成該部位磨損較大。
4、結(jié)論
通過研究環(huán)模壓塊機(jī)環(huán)模在工作過程環(huán)模內(nèi)側(cè)以及模孔中受力情況,分析模孔間的楔形部位為關(guān)鍵受力部位,應(yīng)用ANSYS軟件分析環(huán)模楔形部位受力后應(yīng)力分布及形變,得出以下結(jié)論:
(1)通過對(duì)環(huán)模在工作過程中環(huán)模內(nèi)側(cè)與壓輥受力情況及物料在模孔中與孔壁受力情況的研究,分析壓塊機(jī)環(huán)模的關(guān)鍵受力部位,得出環(huán)模模孔間的楔形部位為主要受力部位。
(2)應(yīng)用ANSYS軟件分析環(huán)模壓塊機(jī)在工作過程中關(guān)鍵受力的楔形部位應(yīng)力分布及形變,楔形部位軸向內(nèi)側(cè)所受應(yīng)力較大,該部位頂端單側(cè)發(fā)生變形因而較易磨損,在周期載荷作用下疲勞斷裂也是環(huán)模楔形部位的一種失效形式。
(3)根據(jù)對(duì)仿真后得出的環(huán)模受力情況進(jìn)行研究,環(huán)模的楔形部位失效主要為單側(cè)磨損,物料均勻分布有利于改善受力。
(轉(zhuǎn)載請注明:富通新能源秸稈壓塊機(jī)www.hbwcty.com)